Термообработка. Что такое хорошо и что такое плохо.
Как правило, покупая нож, типичный клиент обязательно задаст два вопроса:
1. Из какой стали нож?
2. Какая жесткость?
То есть даже неспециалист где-то в глубине души понимает, что железные железы бывают разные и обработать их можно по-разному. Последнее, правда, явно не всем.
Какой метод термообработки выбрать (азотирование, закалка, ТВЧ, цементация)?
Все зависит от изделия и его эксплуатации.
- Цементация используется при повышенных нагрузках деталей, шестерен с высокими оборотами. Но не все стали цементированы.
- ТВЧ (термическая вакуумно-конденсационная закалка) - локальная термообработка, производится на деталях на которых необходимо закалить какую-то часть шейки, зубы на звездочке и т.д.
- Объемная закалка – закаливается вся деталь, но возможны поводки после термообработки, все зависит от выбранного материала.
- Азотирование металлов – дает высокую жесткость свыше 60 HRC, хорошо выдерживают трение, но слой азотирования получается относительно небольшой, не все материалы подходят под азотирование.
Цементация стали – вид химико-термической обработки , заключающийся в поверхностном диффузном насыщении малоуглеродистой стали углеродом с целью повышения твердости и износостойкости . Цементация с последующей термической обработкой одновременно повышают и предел выносливости .
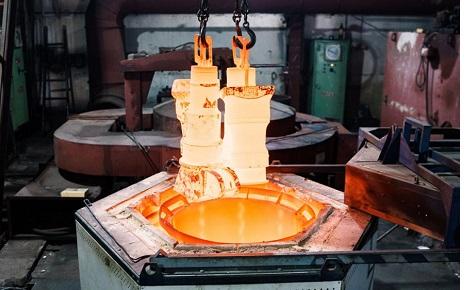
Цементации подвергают малоуглеродистые и легированные стали. Процесс при использовании твердого карбюризатора проводится при температурах 900…950 °С , при газовой цементации (газообразный карбюризатор) — при 850…900 °С.
После цементации изделия подвергают термообработке ( закаливанию ), что приводит к образованию мартенситной фазы в поверхностном слое изделия (закалка на мартенсит) с последующим отпуском для снятия внутренних напряжений .
Очень часто можно увидеть на форумах высказывания типа "Я вот купил нож с 95Х18 - полное гумно, о колбасе крошится, на масле тупится". И тут же – "Да ты гонишь, я своим троих кабанов разобрал и хотя бы хны". Вообще, степень удовлетворенности ножом пользователя – вопрос крайне многогранный, но он включает и сталь и ее ТО. Которая может быть разной. Иногда сильно.
Закалка с применением ТВЧ (термическая вакуумно-конденсационная закалка) - является самым распространенным видом поверхностного укрепления.
В связи с быстрым нагреванием жесткость на поверхности детали на 2-4 единицы больше, чем при объемном закаливании.
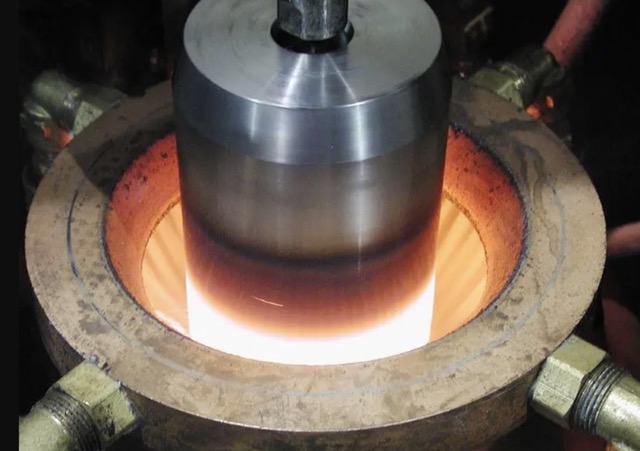
Сырая, вязкая сердцевина способствует уменьшению хрупкости.
Глубина закаленного слоя колеблется от 1 мм до 5 мм.
tvch vtulka
Установка ТВЧ состоит из высокочастотного генератора, трансформатора и самого индуктора.
Индуктор производят из медной трубки. Тип индуктора зависит от формы и размера детали.
Чаще всего внешний вид наиболее распространенного индуктора напоминает катушку, которая может иметь один или несколько витков.
Объемно-поверхностная закалка (металлов) – это закалка, при которой глубина прокаливания регулируется химическим составом стали и режимом индукционного нагрева; глубина залегания полумартенситного слоя при этом 0,15-0,25 диаметра или толщины изделия.
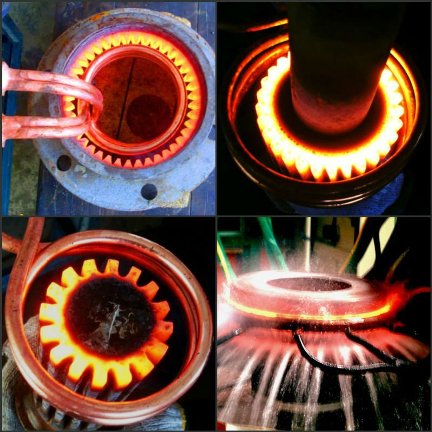
Технология ОПЗ имеет целый ряд преимуществ перед аналогичными российскими и зарубежными аналогами, по многим из которых она превосходит ближайшие аналоги в 3-10 раз.
Основными преимуществами являются:
- Крайне высокий срок службы изделий.
- Цикл закалки со стандартных 12-20 часов до 1-5 минут.
- Отсутствуют термические деформации деталей после их термообработки.
- Стоимость одной стали пониженной прокаливаемости, значительно ниже легированной стали.
- Снижение потребности в электроэнергии в 10-12 раз.
- Возможность регулировки заданных параметров в разных местах одного изделия.
- Возможность регулировки срока службы изделий.
- Абсолютная экологичность.
Основные сферы применения технологии ОПЗ: укрепление деталей бурового оборудования, деталей шарико-подшипниковой группы, шестерен, валов, рессор и т.д.
Азотирование металлов (интригование, но не путать с нитрованием в органической химии) — вид химико-термической обработки, который заключается в насыщении азотом поверхностного слоя металлических изделий для повышения твердости, стойкости против срабатывания, выносливости и коррозионной стойкости в различных агрессивных средах.
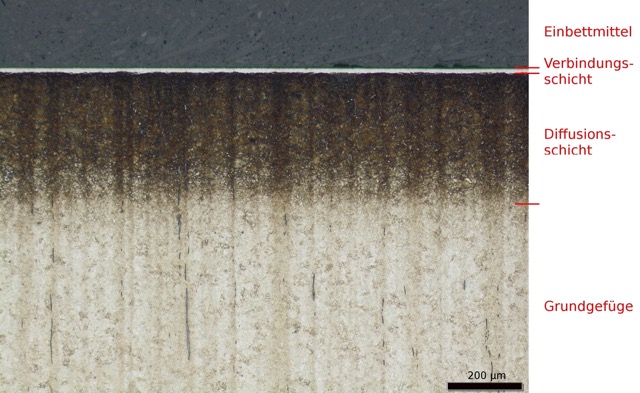
Прочное азотирование изделий производят при температуре 500…600 °C в камерных, шахтных, контейнерных или колпаковых печах, в которые подают струю сухого аммиака. В печи аммиак распадается на водород и азот. Легирующие элементы (алюминий, молибден, ванадий, хром) образуют с азотом устойчивые химические соединения — нитриды, придающие изделиям большую жесткость (1200 по Виккерсу). Толщина азотированного слоя составляет 0,3…0,6 мм при выдерживании в печи от 24 до 90 часов.
Азотирование повышает жесткость поверхностного слоя, износостойкость, выносливость и коррозионную стойкость стальных изделий. Азотированный слой имеет твердость 700…1200 HV (58…72 HRC), которая сохраняется при рабочих температурах до 600 °C.
Азотированию подвергают цилиндры и клапаны двигателей, зубцы шестерен, седла к клапанам, шпиндели и ходовые винты быстроходных станков и т.п. Азотирование повышает также стойкость измерительного инструмента, применяемого в машиностроении (резьбовые пробки и кольца, плоские калибры, скобы, шаблоны и т.п.). Азотирование изделий производят после механической и термической обработки.
Антикоррозионному азотированию (температура 600…700 °С) подвергают также изделия из углеродистой стали с образованием азотированного слоя толщиной 0,01…0,04 мм при выдерживании в печи в течение 15 мин для мелких деталей и до 10 часов — для крупных.
Так что такое термообработка и с чем ее едят?
Ну, уже из названия понятно, что этим термином описывается множество методов обработки материалов, основанных на изменении их структуры (и соответственно свойств) под влиянием температур. Часто в применении к готовому изделию все это часто называют "закалкой", хотя собственная закалка является лишь одним из этапов. Иногда, приплетая сюда еще и горячую деформацию, все это называют ТМО (термомеханическая обработка), что в большинстве своем коренным образом неверно. Обычно термообработка включает несколько этапов (иногда – несколько десятков). Все они имеют разные цели и разные режимы. Путаницы добавляет еще и то, что в теории термической обработки и на практике довольно часто отдельные процессы имеют разные названия в зависимости от цели и места в технологическом цикле. Вдаваться в дебри не будем, нам, скорее, важны основные этапы и их режимы с точки зрения влияния на конечный результат.
Думаю, что будет проще разобрать это на примере типичной технологии производства клинков (с указанием основных технологических процессов), применяемой подавляющим большинством российских (да и мировых тоже) производителей. Рассмотрим типовую схему, применяемую мастерами-частниками и мелкосерийным производителем.
КОВАНИЕ – один из видов обработки металлов давлением, которое основывается на способности металлов пластически деформироваться – изменять форму, не разрушаясь, под действием внешних сил. Ковке подвергают металлы и сплавы, имеющие достаточно высокую пластичность и низкое сопротивление деформации. Во время ковки осуществляют многократное прерывистое ударение заготовки специальным инструментом. Обычно ее устанавливают незакрепленной на наковальне или в подложенном штампе.
1. Нормализация (иногда + высокий отпуск)
(вырезание бланков)
2. Отжиг или ТЦО.
3. Закалка с МКО
4. Высокий отпуск
5. Закалка
6. Криообработка
7. Результирующий отпуск
(Черновая шлифовка)
8. Отпуск после шлифования
(чистовая шлифовка и доводка)
В случае, если обрабатывается резкой, могут быть дополнительные отпуска (или отжиги).
При массовом производстве одинаковых деталей чаще применяют штамповку или прессование. Основные операции при ковке:
При осаждении материал расплющивают – ширину и длину увеличивают, а толщину уменьшают до тех пор, пока ему не придадут необходимых размеров и формы;
При высадке создают утолщение в результате уменьшения длины. В процессе ручной или машинной ковки. используют основные, поддерживающие и измерительные инструменты.
- протягивание,
- раскат,
- прошивка,
- резка,
- гибки и исправления.
Среди основных инструментов для ручной ковки – кувалда, молотки, ручники, бородки, зубила, обжимы, отбойники; среди основных машинных инструментов – бойки (плоские, фасонные, скругленные, комбинированные), плиты, прошивные. В качестве поддерживающих инструментов при ручной ковке используют клещи, стояки, при машинном – клещи, патроны. Заготовками для ковки могут быть слитки, сортовой и профильный прокат, листы и т.п. Стальные заготовки перед ковкой предпочтительно нагревают в пламенных или разного типа электрических печах до температуры 1100–1250 °С.
Преимущества обработки металлов ковкой по сравнению с резкой:
- меньший (около 30%) расход металла на изделие;
- более высокая производительность оборудования;
- металл становится более плотным по своей структуре.
Ковка без нагрева была известна еще во времена позднего неолита, с помощью него осуществляли обработку самородков металлов (меди, золота, серебра, метеорит. железа).
Рассмотрим влияние отдельных этапов на свойства и качество изделий.
1. Нормализация (иногда + высокий отпуск) – позволяет привести структуру стали к общему знаменателю от которого можно танцевать дальше, снять напряжения, измельчить зерно, в отдельных случаях убрать карбидную сетку или получить необходимую для обработки твердость. Осуществляется в виде нагрева до температур выше температуры фазовых превращений (часто к температурам, вызывающим заметное растворение карбидов) и охлаждение на спокойном воздухе. Многие стали при этом способны поджариваться и получать высокую жесткость – в этом случае добавляют высокий отпуск.
2. Отжиг или ТЦО – позволяет измельчить зерно, снизить твердость до минимальных значений (для обработки резкой или холодной деформации), снять остаточное напряжение. Осуществляется нагревом до температур несколько выше температур фазовых превращений (в отдельных случаях – межкритическая область) и медленным охлаждением до температур окончания перлитного распада. Часто отжиг выгодно заменять термоциклической обработкой – многократным повторением циклов нагрева-охлаждения до температур соответственно выше/ниже температур фазовых превращений. Такая обработка позволяет заметно в большей степени измельчить зерно и в результате получить заметно самый лучший мех. Свойства.
3. Закалка из МКО. Позволяет значительно уменьшить поводки и коробку деталей, благодаря закрытию микропор в отдельных случаях несколько повышает жесткость и мех. характеристики сталей. Выполняется как "мягкая" закалка из межкритической области, как правило, охлаждением в масле.
4. Высокий отпуск (с точки зрения теории ТО – докритический отжиг) – снимает напряжения после меха. обработки, подготавливающей структуру стали к закаливанию, в отдельных случаях снижает твердость стали до минимальных значений.
5. Закалка – основной этап ТО. Состоит в нагревании до температур, выше температур фазовых превращений и как правило, вызывающих заметное растворение карбидов, создающих необходимое насыщение твердого раствора углеродом и легирующими элементами и быстрое охлаждение (со скоростью выше критической), фиксирующие этот твердый пересыщенный раствор.
6. Криообработка – охлаждение изделия до низких температур (как правило -78 – 196С). Целью возможно более полное преобразование остаточного аустенита, что увеличивает твердость, устойчивость к смятию и уменьшает риск преобразования аустенита при эксплуатации, но может снижать вязкость.
7. Результирующий отпуск – формирует окончательные свойства клинка. Обычно осуществляют нагрев до относительно невысоких температур (иногда средних температур). При закаливании на вт
8. Отпуск после шлифования – снимает шлифовальные напряжения и иногда стабилизирует аустенит, образовавшийся при шлифовании.
Не все этапы не всегда необходимы, некоторые могут частично или полностью заменять друг друга – все зависит от стали и технологического цикла. В случае покупки полуфабрикатов заметная часть ТО уже сделана на предприятии – изготовителе.
Обычно этапы ТО делят на предварительную и результирующую ТО. Результирующая ТО формирует свойства готового изделия (как правило, это все, начиная с последней высокотемпературной степени – закалки), задача ПТО – обеспечить необходимые технологические свойства и подготовить структуру к результирующей ТО.
Конечно, именно результирующая ТО больше всего влияет на "базовые" свойства стали, но именно ПТО часто позволяет "выдавить" из стали максимум того, на что она способна.
Конечно – бесплатных пирожных не бывает. С усложнением ТО возрастают трудозатраты, загрузка оборудования и т.д. Что неизбежно приводит к росту цен на изделия. Часто многократном. Поэтому излишне оптимистично искать бриллианты среди ширпотреба. С другой стороны, попытки выжать максимум могут привести к таким затратам, что изделие приобретает статус "эксклюзива" с соответствующей ценой. Надо где-нибудь остановиться. Где именно – каждый производитель решает себе сам. Вернее – там, где останавливается его целевой покупатель.
Рассмотрим главные варианты.
1. Сковал, нагрел в горне до ярко-оранжевого, засунул в масло. Подержал над углем 5 минут – обитателю, все… В этом случае рассчитывать хотя бы на средний для этой стали результат достаточно оптимистично. При огромном опыте возможно все…
2. Отдал "какому-нибудь термисту" с оборонного завода. Что и как тот с железной дорогой делал – тайна эта велика… Результат – от полного отстоя до очень неплохо, правда с заметным преимуществом первого. Кадры решают все.
3. Есть печка, есть "даташит", есть полоска буржуйской стали. Знаний и понимание чего и как нет. Если особенно сильно не косить, то можно получить хороший результат. Особенно с современными сталями – они, как правило, достаточно толерантны к ошибкам.
4. То же + минимальные представления о том, что, куда и зачем. Как правило, при накоплении и осмыслении собственного и чужого опыта и личной ответственности возможно получение стабильно хороших результатов.
5. Есть четкие представления о предмете и/или огромном личном опыте. Плюс заинтересованность в результате и личная ответственность. Это предпосылки для получения стабильных результатов заметно выше среднего. Авторские схемы ТО часто позволяют выжать из сталей заметно больше того, чего от них ждут.
6. Клинки – чемпионы требуют еще и некоторой доли удачи.
Рассмотрим основные ошибки при ТО и их влияние на качество изделия.
1. Недостаточная твердость – как правило, следствие недогрева при закаливании (редко – перегревание) или чрезмерно высоком отпуске. В умеренных формах встречается на недорогих ножах как компенсатор излишне упрощенной ТО.
2. Чрезмерная жесткость и хрупкость "Перекал". А вот здесь все посложнее. Часто речь идет не о высокой жесткости, а о перегревании при закаливании (или непроведенном ПТО), когда сталь получает слишком большое зерно. Собственно, твердость не является единственным показателем качества ТО – к одной и той же жесткости можно прийти разными путями и с разным результатом. Так что утверждение типа "Нож выше 58HRc хрупкое как стекло" надо воспринимать со здоровым скепсисом.
3. Безуглеродный слой. При отсутствии защитных атмосфер/покрытий или вакуумного оборудования практически всегда. При пищеварении обычно выглядит заметно светлее фона. При правильном планировании техпроцесса этот слой удаляется, но в отдельных случаях (например, при закаливании тонко сведенной заготовки или выполнении ножа со "стамесочной" заточкой без удаления обезуглероженного слоя) он может выходить на ЖК, с самыми печальными последствиями для последней. Иногда он может стать причиной ошибок по твердости – там она будет заметно меньше, чем на теле клинка и ЖК.
4. Трещины. Могут появиться на разных этапах производства, чаще всего при ковке, закаливании или шлифовании. Является безусловным неисправимым браком. Продажа такого клинка (за исключением ОЧЕНЬ редких случаев на многослойных мечах или дамасках) – прямое указание на отношение производителя к делу. Хреновое отношение.
5. Поводки и коробление. На длинномере они практически неизбежны, на коротком мече допустимы в известной степени.
В заключение несколько реальных историй о разных ножах.
1. Проводя закалку кузнец А свинчивает несколько десятков заготовок шпильками, бросает в печь, идет пить водку. Через несколько часов возвращается, бросает бутерброд в бак с маслом, идет пить водку. Отпуска не делает – а зачем там и так 58…
2. Кузнец Б в течение многих лет калит Х12МФ с температур на 50 градусов выше оптимальных. На резонный вопрос о причинах - "Я всегда так делаю, люди не жалуются".
3. Энтузиаст В решил провести криообработку путем закалки раскаленной до 1175 г. заготовки в жидком азоте. По предложению сначала найти значение теплоты испарения для жидкого азота за два дня задумчиво высказал "бля".
4. Кузнец Г калит каждую заготовку по-разному. При этом сам их не ощущает и систематически не собирает отзывы. Ищет человек…
5. Мастер Д при закаливании КАЖДОГО клинка кроме авторской ТО и проверки на жесткость всегда контролирует излом – на всякий случай. Вот это – заявка на ответственное отношение к делу, которое проявляется в других вопросах и находит отражение в цене изделий.
Так что, выбирая ТО вы выбираете ПРОИЗВОДИТЕЛЯ. У разных мастеров могут быть разные взгляды на ТО, но ответственный и уважающий себя и потребителя производитель никогда не выпустит в продажу изделие со свойствами ниже некоторого минимума. А в случае брака (чего не бывает) приложит максимум усилий к разрешению ситуации.
Процессы термической обработки стали
Стали можно подвергать термической обработке для получения широкого спектра микроструктур и параметров. Как правило, термическая обработка использует фазовое преобразование при нагревании и охлаждении для изменения микроструктуры твердого состояния. При термической обработке обработка, как правило, термическая и изменяет только структуру стали. При термомеханической обработке сталей форма и структура стальных компонентов также изменяются. При термохимической обработке сталей химический состав поверхности и структура стали модифицируются. Процессы термомеханической и термохимической обработки также являются важными подходами к термической обработке стали и рассматриваются в области термической обработки. Процесс термической обработки требует тщательного контроля за всеми факторами, влияющими на нагрев и охлаждение стали. Атмосфера нагревательной печи также влияет на состояние подвергающейся термической обработке стали.
Все процессы термической обработки состоят из подвергания стали определенному температурно-временному циклу. Этот временно-температурный цикл состоит из трех компонентов, а именно (i) нагревания, (ii) выдерживания в определенном диапазоне температур (замачивания) и (iii) охлаждения. Отдельные случаи могут отличаться, но некоторые фундаментальные цели есть.
Скорость нагрева детали зависит от нескольких факторов. Эти факторы: (i) теплопроводность стали, (ii) состояние стали и (iii) размер и поперечное сечение стали. Важным фактором является теплопроводность стали. Сталь с высокой теплопроводностью нагревается быстрее сталь с низкой теплопроводностью. Скорость нагрева не особенно важна, если только сталь не находится в состоянии сильной нагрузки, например, в результате сильной холодной обработки или предварительной закалки. В таких случаях скорость нагрева должна быть медленной. Часто это практически невозможно, поскольку печи, используемые для нагревания, могут иметь рабочую температуру, а размещение холодной стали в горячей печи может привести к деформации или даже растрескиванию. Эту опасность можно свести к минимуму, используя печь предварительного нагрева, поддерживаемую при температуре ниже температуры A1 на фазовой диаграмме железо-углерод (рис. 1). Сталь, предварительно нагретая в течение достаточного времени, затем перемещается в печь, находящуюся при рабочей температуре. Эта процедура также полезна при обработке сталей со значительными колебаниями толщин профиля или очень низкой теплопроводностью.
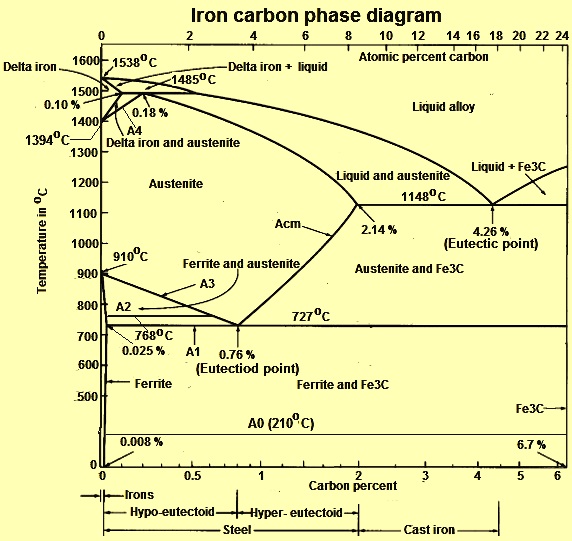
Рис. 1. Фазовая диаграмма железо-углерод
После того, как стальной профиль нагревается до положенной температуры, его выдерживают при этой температуре, пока не произойдут желаемые внутренние структурные изменения. Этот процесс называется «замачивание». Период выдержки при должной температуре называется периодом замачивания. Задача замачивания – обеспечить равномерность температуры по всему объему. Очевидно, что тонкие срезы не нужно замачивать так долго, как толстые срезы, но если одна и та же стальная деталь разной толщины, время, необходимое для равномерного нагрева самого толстого среза, решит время при температуре. Как правило, примерно 30 минут замачивания необходимо для среза толщиной 25 мм.
После того, как стальной профиль замачивается, его следует вернуть до комнатной температуры для завершения процесса термической обработки. Для охлаждения металла можно использовать хладагент. Охлаждающая среда может состоять из газа, жидкости, твердого вещества или их комбинации. Скорость охлаждения стального профиля зависит от стали и желаемых свойств. Скорость охлаждения зависит от охлаждающей среды, а значит, выбор охлаждающей среды оказывает важное влияние на необходимые свойства. Микроструктура и свойства стали зависят от скорости охлаждения стали, что, в свою очередь, определяется такими факторами, как масса, среда для закалки и т.д. Следует понимать, что чем толще профиль стали, тем медленнее скорость охлаждения независимо от используемого метода охлаждения, за исключением таких операций, как индукционное закаливание.
Различные типы процессов термической обработки схожи, поскольку все они включают нагрев и охлаждение стали. Однако процессы отличаются по используемым температурам нагрева и скорости охлаждения и конечным результатам. Нормальными процессами, используемыми для термической обработки стали, являются (i) отжиг, (ii) нормализация, (iii) закалка и (iv) отпуск.
Отжиг
Отжиг – это процесс термической обработки, включающий нагрев и охлаждение. Процесс обычно используется для размягчения стали. Термин также относится к обработкам, направленным на изменение механических или физических свойств, созданию определенной микроструктуры или удалению газов. Температура операции и скорость охлаждения зависят от типа отжигаемой стали и цели обработки. Различные типы процессов отжига описаны ниже.
Полный отжиг – это процесс размягчения, во время которого стальной профиль нагревается до температуры, превышающей диапазон аустенитного преобразования, и после выдерживания в течение достаточного времени при этой температуре медленно охлаждается до температуры ниже диапазона преобразования. Стали, как правило, позволяют медленно остыть в печи, хотя ее можно вынуть и охладить в какой-либо охлаждающей среде. Поскольку на температуре превращения влияет содержание углерода в стали, очевидно, что высокоуглеродистые стали можно полностью отжечь при более низких температурах, чем низкоуглеродистые стали. Микроструктура доэвтектоидных сталей, образующихся после полного отжига, состоит из феррита и перлита. Эвтектоидные и заевтектоидные стали часто частично или полностью сфероидизуются при полном отжиге.
Технологический отжиг – технологический отжиг также часто называют отжигом для снятия напряжения. Процесс обычно используется для холодной обработки стали с низким содержанием углерода (приблизительно до 0,25 % углерода) для достаточного размягчения стали для дальнейшей холодной обработки. Сталь обычно нагревается близко к температуре А1, но ниже ее. Если сталь не подлежит дальнейшей холодной обработке, но требуется снятие внутреннего напряжения, достаточен низкий диапазон температур (приблизительно 540 °C). Здесь не важна скорость охлаждения. Этот тип отжига вызывает рекристализацию и размягчение холоднообработанных ферритовых зерен, но обычно не влияет на относительно небольшое количество холоднообработанного перлита.
Сфероидизация
Сфероидизация – это процесс нагрева и охлаждения стали, образующий округлую или шаровидную форму карбида в матрице феррита. Обычно это осуществляется путем длительного нагревания при температурах чуть ниже температуры A1, но его можно облегчить путем поочередного нагревания до температур немного выше температуры A1 и охлаждения до температуры немного ниже A1. Последний этап, однако, состоит из выдержки при температуре чуть ниже критической температуры A1. Скорость охлаждения не важна после медленного охлаждения приблизительно до 540 °C. На скорость сфероидизации влияет начальная структура. Чем мельче перлит, тем легче происходит сфероидизация. Мартенситная структура очень восприимчива к сфероидизации. Эта обработка обычно используется для высокоуглеродистых сталей (0,60% углерода и выше). Целью этой обработки является улучшение обрабатываемости стали. Процесс также используется для кондиционирования высокоуглеродистой стали для холодного извлечения проволоки.
Нормализация
Нормализованная обработка часто применяется к стали для достижения какой-либо одной или нескольких из этих целей, а именно (i) для улучшения зернистой структуры, (ii) для получения однородной структуры, (iii) для уменьшения остаточных напряжений и (iv) улучшить обрабатываемость стали .
Нормализация – это процесс, во время которого сталь нагревают до температуры, превышающей температуру A3 или Acm, а затем охлаждают в атмосферном воздухе. Целью нормализующей обработки является устранение последствий любой предварительной термической обработки (включая крупнозернистую структуру, которая иногда является результатом высоких температур ковки) или холодной обработки. Процесс нормализации выполняется для обеспечения однородного аустенита при повторном нагреве для закалки или полного отжига. Полученные структуры являются перлитовыми или перлитовыми с избытком феррита или цементита в зависимости от состава стали.
Структуры после нормализации отличаются от структур, полученных после отжига, и сталей с одинаковым содержанием углерода в заэвтектоидном или заэвтектоидном диапазонах, там меньше избытка феррита или цементита, а перлит более мелкий. Это результаты более быстрого охлаждения. Поскольку на тип структуры, а следовательно, и на механические свойства влияет скорость охлаждения, в нормализованных сталях могут иметь место существенные вариации из-за разницы в толщине нормализованного сечения форм.
Закаливание
Стали можно закалить простым средством нагрева стали до температуры выше температуры преобразования А3, выдерживание достаточно долго, чтобы обеспечить достижение равномерной температуры и растворение углерода в аустените, а затем быстрое охлаждение стали (закалка). Полное укрепление зависит от охлаждения настолько быстро, что аустенит, который не разлагается при охлаждении из-за температуры А1 и поддерживается при относительно низких температурах. Когда это достигается, аустенит начинает превращаться в мартенсит при охлаждении ниже температуры Ms (приблизительно 220 °C) и полностью превращается в мартенсит ниже температуры Mf. Быстрое охлаждение необходимо только для того, чтобы температура стали снизилась значительно ниже верхней части S-кривой (рис. 2). Когда это достигнуто, медленное охлаждение с этого момента, либо в масле, либо на воздухе, полезно во избежание деформации и растрескивания. Специальные методы обработки, такие как закалка со временем и закалка, предназначены для достижения этих условий. Поскольку мартенсит достаточно хрупок, сталь редко используется в закаленном состоянии, то есть без отпуска. Максимальная жесткость, которой можно достичь в полностью закаленных низколегированных сталях и простых конструкционных углеродистых сталях, зависит в первую очередь от содержания углерода.
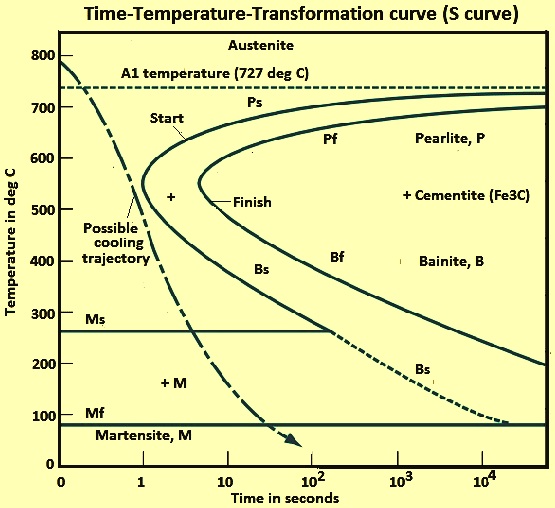
Рис. 2 Кривая преобразование время-температура
Воздействие массы – масса стали влияет на формирование мартенсита. Видно, что даже при относительно небольших размерах образца скорость отвода тепла неравномерна. Тепло всегда удаляется из поверхностных слоев быстрее, чем из внутреннего снадобья. В данной охлаждающей среде скорость охлаждения как поверхности, так и внутренней части уменьшается с увеличением размеров образца и возможность превышения критической скорости охлаждения становится меньше. Чтобы преодолеть это, сталь нужно закалить в среде, которая имеет очень высокую скорость отвода тепла, например, охлажденной рассоле, но, несмотря на это, многие стали имеют физическое ограничение на максимальный размер, чувствительный к полной закале независимо от этого. среды гашения. Заметное влияние массы на жесткость закаленной стали можно продемонстрировать, измерив распределение твердости различных по размеру заготовок той же стали, закаленной в одной среде.
Воздействие углерода – Содержание углерода в простых углеродных и низколегированных сталях влияет на температуру преобразования Ms. При увеличении содержания углерода температура Ms снижается (рис. 3).
Рис. 3 Воздействие углерода на температуру Ms
Закаливание
Отпуск (иногда его называют вытягиванием) — это процесс повторного нагрева закаленной (мартенситной) или нормализованной стали до температуры ниже температуры А1. Скорость охлаждения не имеет значения, за исключением некоторых сталей, чувствительных к отпускной хрупкости. По мере повышения температуры отпуска мартенсит закаленной стали проходит через стадии отпущенного мартенсита и постепенно превращается в структуру, состоящую из сфероидов цементита в матрице феррита (ранее назывался сорбит). Эти изменения сопровождаются уменьшением жесткости и повышением ударной вязкости.
Температура отпуска зависит от желаемых свойств и целей, для которых будет использоваться сталь. Если необходима значительная жесткость, то температура отпуска должна быть низкой. С другой стороны, если требуется значительная вязкость, температура отпуска должна быть высокой. Правильный отпуск закаленной стали требует определенного времени. При любой выбранной температуре отпуска жесткость сначала быстро падает, постепенно уменьшаясь медленнее по мере продления времени. Короткие периоды закаливания обычно нежелательны, поэтому их следует избегать. Хорошая практика требует не менее 30 минут (или лучше 1-2 часа) при температуре отпуска для любой закаленной стали.
Невозможно переоценить необходимость закаливания стали сразу после закалки. Если полностью закаленная сталь остынет до комнатной температуры во время закалки, существует опасность растрескивания стали. Углеродистые стали и большинство низколегированных сталей нужно отпускать, как только они достаточно охладятся, чтобы их было удобно держать в руках. Стали нельзя отпускать до того, как они охладятся до этой температуры, поскольку в некоторых сталях температура Mf достаточно низкая и может присутствовать непревращенный аустенит. Часть всего этого остаточного аустенита превращается в мартенсит при охлаждении от температуры отпуска, так что конечная структура состоит как из отпущенного, так и неотпущенного мартенсита. Хрупкий неотпущенный мартенсит вместе с внутренними напряжениями, вызванными его образованием, могут легко повлечь за собой разрушение термически обработанной стальной детали. Если возможно, что такое условие существует, необходимо провести второй отпуск (двойной отпуск) для отпуска нового мартенсита, который образовался при охлаждении после начального отпуска.
Если конструкционные стали должны использоваться в нормализованном состоянии, операция нормализации часто сопровождается нагреванием до температуры от приблизительно 650 до 700C. Целью этой обработки, которая также обозначается как отпуск, является освобождение внутреннего напряжения, возникающего при охлаждении от температуры нормализации, и для улучшения пластичности стали.
Укрепление корпуса
Закаливание цемента – это процесс закаливания черных сплавов таким образом, что поверхностный слой или корпус становится значительно жестче, чем внутренний слой или сердечник. Химический состав поверхностного слоя изменяется при обработке добавлением углерода, азота или обоих. Наиболее распространенными процессами цементирования являются науглероживание, цианирование, карбоназотирование и азотирование.
Цементация – это процесс, вводящий углерод в твердый сплав железа путем нагревания металла в контакте с углеродным материалом до температуры, превышающей температуру A3 стали, и выдерживания при этой температуре. Глубина проникновения углерода зависит от температуры, времени нахождения при температуре и состава цементирующего агента. Как примерный показатель, глубина углерода примерно от 0,75 мм до 1,25 мм может быть достигнута примерно за 4 часа при 930 °C, в зависимости от типа углерода, который может быть твердым, жидким или газообразным. Поскольку основной целью науглероживания является получение твердого корпуса и относительно мягкого, крепкого сердечника, используйте только низкоуглеродистые стали (не более 0,25 % углерода), с легирующими элементами (никель, хром, марганец) или без них. или молибден) обычно используются. После цементации сталь имеет высокоуглеродистый корпус, переходящий в низкоуглеродистое ядро.
После науглероживания можно использовать различные термические обработки, но все они включают закалку стали для укрепления поверхностного слоя. Простейшая обработка заключается в закаливании стали непосредственно от температуры цементации. Эта обработка укрепляет как корпус, так и сердечник (насколько сердечник можно закалить). Другая простая обработка, и, пожалуй, наиболее часто используемая, заключается в медленном охлаждении от температуры углерода, повторном нагревании до температуры выше A3 корпуса (примерно 775 °C) и закалки. Такая отделка только укрепляет корпус. Более сложная обработка заключается в двойной закалке, состоящей из первой закалки выше температуры A3 сердцевины (примерно 900 °C для низкоуглеродистой стали), а затем от температуры выше A3 корпуса (около 775 °C). Эта обработка очищает сердечник и укрепляет корпус. Обычные углеродистые стали почти всегда закаляются в воде или рассоле, тогда как легированные стали обычно закаляются в масле.
Хотя отпуск после закалки цементированной стали иногда пропускают, низкотемпературный отпуск приблизительно при 300 С является хорошей практикой. Иногда желательно науглероживать только отдельные части поверхности. Это можно сделать, покрыв поверхность, которую нужно защитить от науглероживания, некоторым материалом, препятствующим прохождению углерода. Самым распространенным методом является меднение защищаемых поверхностей. Также доступны несколько запатентованных растворов или паст, которые достаточно эффективно предотвращают науглероживание. Коммерческие смеси, обычно используемые для упаковочного (твердого) цементирования, содержат смеси карбоната (обычно карбоната бария), кокса (разбавитель) и древесного угля из лиственных пород с маслом, смолой или патокой как связующим веществом. Используются также смеси обугленной кожи, кости и древесного угля. Науглероживающее действие этих соединений уменьшается при использовании, поэтому перед повторным использованием смеси необходимо добавить новый материал. Добавление одной части неиспользованной смеси к трем-пяти частям использованной смеси является обычной практикой.
Детали, подлежащие науглероживанию, упаковывают в ящики (или другие соответствующие контейнеры), изготовленные из жаростойких сплавов, хотя можно использовать прокат или литую сталь, где долговечность ящика неважна. Верхнюю крышку коробки нужно закрыть шамотной глиной или другим огнеупорным материалом, чтобы предотвратить утечку углеродящегося газа, который образуется при температуре науглероживания. На глубину и однородность корпуса оказывает влияние способ упаковки и конструкция тары. Жидкое цементирование состоит из закалки стали или чугуна в расплавленных соляных ваннах, содержащих смеси в основном цианидов (очень ядовитых), хлоридов и карбонатов. Корпус, получаемый этим методом, содержит как углерод, так и азот, но главным образом первый. Используемые температуры колеблются от примерно 850 до 900 °C или выше, в зависимости от состава ванны и желаемой глубины корпуса. При 900 °C глубину корпуса от приблизительно 0,25 мм до приблизительно 0,4 мм можно достигнуть за 1 час, а приблизительно от 0,5 мм до 0,75 мм можно достигнуть за 4 часа. Значительно более глубокие корпуса могут быть получены при более высоких температурах с более длительными периодами времени.
После науглероживания сталь необходимо закалить так же, как и при жестком науглероживании, но обычно это делается непосредственно из расплавленной ванны. Во всех современных коммерческих газовых цементациях два или более углеводородов используются в комбинации для подачи углерода в сталь. В качестве углеводородов используются метан, этан, пропан и пары нефти. Стальные детали помещены в герметичные контейнеры, через которые циркулируют науглероживающие газы. Используемые температуры находятся около 925 °C. Среднее ожидаемое значение глубины корпуса в науглероживаемой стали приведено на рис. 4. После науглероживания сталь подлежит закаливанию.
Рис. 4. Связь времени и температуры с проникновением углерода при газовом науглероживании
Цианирование – жесткий, поверхностный корпус можно быстро получить на низкоуглеродистых сталях путем цианирования. Этот процесс предполагает введение как углерода, так и азота в поверхностные слои стали. Сталь, подлежащую цианидованию, обычно нагревают в расплавленной ванне цианид-карбонат-хлоридных солей (обычно содержит от 30 до 95% цианида натрия), а затем закаливают в рассоле, воде или минеральном масле. Рабочая температура обычно находится в диапазоне от 850 °C до 875 °C. Глубина корпуса зависит от времени, температуры и состава цианидной ванночки. Время погружения относительно короткое по сравнению с науглероживанием обычно варьируется от 15 минут до 2 часов. Максимальная глубина корпуса редко превышает примерно 0,5 мм, а средняя глубина значительно меньше.
Цианидировать стали можно путем нагревания до соответствующей температуры и погружения в порошкообразную цианидную смесь или посыпания порошка на сталь с последующей закалкой. Сформированный таким образом корпус очень тонкий. Цианидирующие соли чрезвычайно ядовиты, если попасть на царапины или раны. При приеме внутрь они смертельно ядовиты. При контакте цианидов с кислотами выделяются смертельно ядовитые пары. Ванны цианирования должны быть оборудованы колпаком для отвода выделяемых газов при нагревании, а рабочее помещение должно хорошо проветриваться. Никогда нельзя допускать контакта расплавленного цианида с нитратами натрия или калия, обычно используемыми для ванн для закалки, поскольку смеси взрывоопасны. Кроме того, необходима осторожность при подготовке соляной ванны и сталь должна полностью высохнуть перед размещением в расплавленной ванне. При эксплуатации и обслуживании соляных ванн необходимо строго соблюдать рекомендации производителей соли.
Карбонитридирование – карбонитридирование также известно как газовое цианидирование, сухое цианидирование и неткарбингование. Это процесс закалки стальной детали в газовой атмосфере, содержащей аммиак в контролируемых процентах. Карбонитрование используется в основном как недорогой заменитель цианирования. Как и в процессе цианирования, в сталь добавляют углерод и азот. Процесс выполняется выше температуры стали A1 и практичен до 925 °C. Закалка в масле достаточно быстро для достижения максимальной жесткости поверхности. Такая умеренная скорость охлаждения минимизирует искажение. Глубина, на которую проникают углерод и азот, зависит от температуры и времени. Проникновение углерода примерно такое же, как и при газовом науглероживании (рис. 3).
Азотирование – процесс азотирования заключается в подвергании механически обработанной и термически обработанной стали без обезуглероживания поверхности действия азотистой среды, обычно газообразного аммиака, при температуре от приблизительно 500 до 540 °C. Очень жесткая поверхность является полученным этим процессом. Эффект поверхностного укрепления обусловлен поглощением азота, поэтому дальнейшая термообработка стали отпадает. Необходимое время относительно длительное обычно составляет от 1 до 2 дней. Корпус даже после 2 дней азотирования, как правило, менее 0,5 мм. И высокая жесткость существует в поверхностных слоях на глубину лишь в несколько сотых миллиметра.
Для азотирования разработаны специальные низколегированные стали. Эти стали содержат элементы, которые легко сочетаются с азотом с образованием нитридов. Наиболее благоприятными из этих элементов являются алюминий, хром и ванадий. Молибден и никель используются в этих сталях для придания крепости и вязкости. Обычно содержание углерода составляет от 0,20 до 0,50%, хотя в некоторых сталях, где необходима высокая твердость сердцевины, он может достигать 1,3%. Нержавеющие стали можно также подвергать азотированию.
Поскольку азотирование производится при относительно низкой температуре, в качестве основного материала целесообразно использовать закаленную и отпущенную сталь. Это дает прочную, прочную сердцевину с интенсивно твердым износостойким корпусом, который действительно намного твердее, чем можно получить путем закаливания карбонизированной или цианидированной стали. Хотя искривление не является проблемой при азотировании, стали немного увеличиваются в размере во время этой обработки. Этот рост можно учесть в готовом изделии. Защита от азотирования может быть достигнута лужением, медением, бронзированием или нанесением некоторых красок.
Поверхностное укрепление
Зачастую приходится укреплять только поверхность сталей без изменения химического состава поверхностных слоев. Если сталь содержит достаточное количество углерода для реагирования на закалку, можно укрепить поверхностные слои только очень быстрым нагреванием в течение короткого периода времени, таким образом подготовив поверхность для укрепления путем закаливания.
Индукционное закаливание – во время индукционной закалки ток высокой частоты пропускается через окружающую сталь катушку, поверхностные слои которой нагреваются электромагнитной индукцией. Глубина, на которую распространяется нагретая зона, зависит от частоты тока (низшие частоты дают большую глубину) и от длительности цикла нагрева. Время, необходимое для нагревания поверхностных слоев до температуры выше A3, удивительно мало и часто составляет всего несколько секунд. Выборочный нагрев (и, следовательно, укрепление) достигается соответствующей конструкцией катушек или индукторных блоков. В конце цикла нагревания сталь обычно закаляют струями воды, проходящими через катушки индуктора. Необходимы точные методы управления работой, т.е. расход энергии, длительность нагрева и скорость охлаждения. Эти функции включены в оборудование для индукционной закалки, которое обычно работает полностью автоматически.
Закалка пламенем – это процесс нагрева поверхностных слоев стали выше температуры преобразования с помощью высокотемпературного пламени с последующей закалкой. Во время этого процесса пламя газа попадает непосредственно на стальную поверхность, которую нужно закалить. Скорость нагрева очень высока, хотя и не так быстра, как при индукционном нагревании. Обычные углеродистые стали обычно закаливают разбрызгиванием воды, тогда как скорость охлаждения легированных сталей может варьироваться от быстрой закалки водой до медленного охлаждения воздухом в зависимости от состава. Любой тип закаленной стали можно закалить пламенем. Для достижения наилучших результатов содержание углерода должно составлять не менее 0,35%, обычный диапазон составляет от 0,40 до 0,50%.
Специальные процессы обработки
Специальные процессы обработки обычно включают отпуск, отпуск и холодную обработку.
Austempering – Austempering – торговое название запатентованного процесса термической обработки. В основном он состоит из нагрева стали до температуры преобразования выше A3, а затем закалки в горячей ванне, поддерживаемой при температуре ниже той, при которой образуется мелкий перлит (конец S-кривой, рис. 2), но выше температуры Ms. как показано на рис. 3. Продуктом изотермического разложения аустенита в этой температурной области является бейнит. Этот компонент сочетает в себе относительно высокую вязкость и жесткость.
Процесс отпуска имеет некоторые ограничения, которые делают его невозможным для использования со многими сталями. Чтобы обеспечить однородную структуру (и, следовательно, однородные свойства), важно, чтобы все поперечное сечение стали достаточно быстро охлаждалось, чтобы даже центр избежал трансформации в конце S-кривой. В углеродных сталях время, необходимое для начала превращения в конце S-кривой, является чрезвычайно коротким, поэтому лишь относительно небольшие секции (около 10 мм максимальной толщины) могут быть успешно закалены горячим способом в ваннах аусгарта. Время, необходимое для превращения аустенита легированных сталей в тонкодисперсный перлит, как правило, более длинное, и, следовательно, большие секции можно успешно подвергнуть аустемперации (около 25 мм максимум). Однако время, необходимое для превращения в бейнит, часто становится чрезмерно длинным для многих легированных сталей, и, следовательно, процесс отпуска обычно невозможен для этих сталей.
Закалка – закалка состоит из нагрева стали до температуры преобразования выше A3, а затем закалка в ванне, поддерживаемая при температуре, примерно равной температуре Ms. Сталь выдерживают в горячей ванне, пока температура не станет равномерной, а затем ее охлаждают на воздухе. При закаливании в стали возникают сильные внутренние напряжения. При охлаждении сталь сжимается, но подвергается заметному расширению, когда аустенит превращается в мартенсит. Поскольку закаленная сталь должна охлаждаться от поверхности внутрь, разные части превращаются в разное время. Таким образом, сталь подвергается разнообразным различным расширениям и сужениям, что приводит к значительным внутренним напряжениям. Благодаря выравниванию температуры по всей секции перед преобразованием, а затем медленному охлаждению через диапазон мартенсита (Ms-Mf), внутренние напряжения значительно уменьшаются, что также является основной целью отпуска.
Холодная обработка – температура Mf многих легированных сталей настолько низка, что полное превращение аустенита в мартенсит не происходит при закаливании до комнатной температуры или охлаждении после отпуска. Этот удержанный аустенит может быть частично или полностью преобразован путем охлаждения ниже атмосферной температуры, и такая обработка называется холодной обработкой. Полезные эффекты лечения холодом до конца не изучены. Понятно, что остаточный аустенит высоколегированных сталей частенько тяжело трансформировать. Охлаждение этих сталей до низких температур (до температуры твердого СО2 или даже ниже) сразу после закалки иногда эффективно для превращения остаточного аустенита, но с связанной с этим опасностью растрескивания. Когда холодную обработку применяют после отпуска, сохраненный аустенит значительно более устойчив к превращению. Если используется холодная обработка, после этого сталь всегда должна быть закалена.
Повторный поочередный нагрев до температуры, немного ниже используемой при закалки, и охлаждение до минусовой температуры в охлажденном рассоле со льдом, углекислый газ, жидкий воздух или жидкий азот обычно используются для превращения остаточного аустенита (стабилизация размеров) стальных калибров, особенно шарикоподшипникового. типа.