Термообробка. Що таке добре і що таке погано.
Як правило, купуючи ніж, типовий клієнт обов'язково поставить два питання:
1. З якої стали ніж?
2. Яка твердість?
Тобто навіть неспеціаліст десь у глибині своєї душі розуміє, що залізні залози бувають різні і обробити їх можна по-різному. Останнє, щоправда, вочевидь не всім.
Який метод термообробки вибрати (азотування, загартування, ТВЧ, цементації)?
Все залежить від виробу та його експлуатації.
- Цементація використовується при підвищених навантаженнях деталей, шестерень із високими оборотами. Але не всі стали цементовані.
- ТВЧ (Термічне Вакуумно-Конденсаційна загартування) - локальна термообробка, робиться на деталях на яких необхідно загартувати якусь частину шийки, зуби на зірочці тощо.
- Об'ємне гартування - гартовується вся деталь, але можливі повідки після термообробки, все залежить від вибраного матеріалу.
- Азотування металів - дає високу твердість понад 60 HRC, добре витримують тертя, але шар азотування виходить відносно невеликий, не всі матеріали підходять під азотування.
Цементація сталі — вид хіміко-термічної обробки, що полягає у поверхневому дифузійному насиченні маловуглецевої сталі вуглецем з метою підвищення твердості та зносостійкості. Цементація з наступною термічною обробкою одночасно підвищують і границю витривалості.
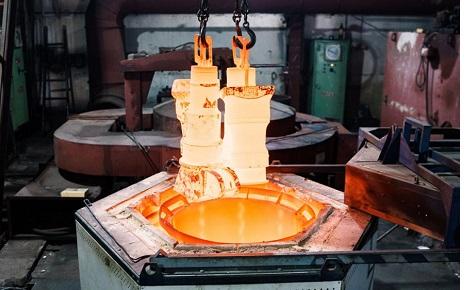
Цементації піддають маловуглецеві і леговані сталі. Процес у разі використання твердого карбюризатора проводиться при температурах 900…950 °С, при газовій цементації (газоподібний карбюризатор) — при 850…900 °С.
Після цементації вироби піддають термообробці (гартуванню), що приводить до утворення мартенситної фази у поверхневому шарі виробу (гартування на мартенсит) з наступним відпуском для зняття внутрішніх напружень.
Дуже часто можна побачити на форумах висловлювання на кшталт "Я ось купив ніж з 95Х18 - повне гумно, про ковбасу кришиться, на олії тупиться". І тут же - "Та ти женеш, я своїм трьох кабанів розібрав і хоч би хни". Взагалі, ступінь задоволеності ножем користувача - питання вкрай багатогранне, але він включає і сталь і її ТО. Яка може бути різною. Іноді сильно.
Загартування із застосуванням ТВЧ (Термічне Вакуумно-Конденсаційна загартування) - є найпоширенішим видом поверхневого зміцнення.
У зв'язку зі швидким нагріванням твердість на поверхні деталі на 2-4 одиниці більша, ніж при об'ємному загартуванні.
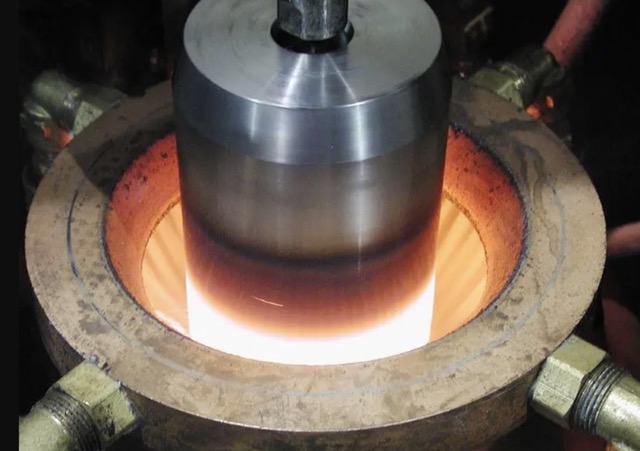
Сира, в'язка серцевина сприяє зменшенню крихкості.
Глибина загартованого шару коливається від 1 до 5 мм.
tvch vtulka
Установка ТВЧ складається з високочастотного генератора, трансформатора та самого індуктора.
Індуктор виготовляють із мідної трубки. Тип індуктора залежить від форми та розмірів деталі.
Найчастіше зовнішній вигляд найпоширенішого індуктора нагадує котушку, яка може мати один або кілька витків.
Об'ємно-поверхневе загартування (металів) - це загартування, при якому глибина прожарювання регулюється хімічним складом сталі і режимом індукційного нагріву; глибина залягання напівмартенситного шару при цьому 015-025 діаметра або товщини виробу.
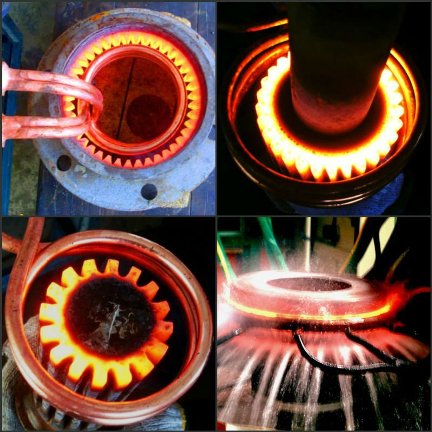
Технологія ОПЗ має цілу низку переваг перед аналогічними російськими та зарубіжними аналогами, за багатьма з яких вона перевершує найближчі аналоги в 3-10 разів.
Основними перевагами є:
- Вкрай високий термін служби виробів.
- Цикл загартування зі стандартних 12-20 годин до 1-5 хвилин.
- Відсутні термічні деформації деталей після їхньої термообробки.
- Вартість однієї сталі зниженої прожарюваності, значно нижча від легованої сталі.
- Зниження потреби у електроенергії в 10—12 разів.
- Можливість регулювання заданих параметрів у різних місцях одного виробу.
- Можливість регулювання терміну служби виробів.
- Абсолютна екологічність.
Основні сфери застосування технології ОПЗ: зміцнення деталей бурового обладнання, деталей кулько-підшипникової групи, шестерень, валів, ресор та ін.
Азотування металів (часом нітрування, але не плутати з нітруванням в органічній хімії) — вид хіміко-термічної обробки, котрий полягає у насиченні азотом поверхневого шару металевих виробів для підвищення твердості, стійкості проти спрацювання, витривалості та корозійної стійкості в різних агресивних середовищах.
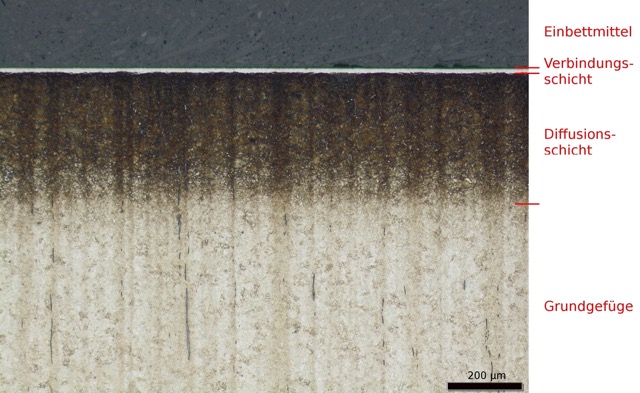
Міцнісне азотування виробів проводять при температурі 500…600 °C у камерних, шахтних, контейнерних або ковпакових печах, в які подають струмину сухого аміаку. В печі аміак розпадається на водень і азот. Легуючі елементи (алюміній, молібден, ванадій, хром) утворюють з азотом стійкі хімічні сполуки — нітриди, які надають виробам великої твердості (1200 за Віккерсом). Товщина азотованого шару становить 0,3…0,6 мм при витримуванні у печі від 24 до 90 год.
Азотування підвищує твердість поверхневого шару, зносостійкість, витривалість і корозійну стійкість сталевих виробів. Азотований шар має твердість 700…1200 HV, (58…72 HRC), яка зберігається при робочих температурах до 600 °C.
Азотуванню піддають циліндри і клапани двигунів, зубці шестерень, сідла до клапанів, шпинделі і ходові гвинти швидкохідних верстатів тощо. Азотування підвищує також стійкість вимірювального інструмента, який застосовується в машинобудуванні (різьбові пробки і кільця, плоскі калібри, скоби, шаблони тощо). Азотування виробів провадять після механічної і термічної обробки.
Антикорозійному азотуванню (температура 600…700 °С) піддають також вироби з вуглецевої сталі з утворенням азотованого шару завтовшки 0,01…0,04 мм при витримуванні у печі протягом 15 хв для дрібних деталей і до 10 год — для великих.
То що таке термообробка і з чим її їдять?
Ну, вже з назви зрозуміло, що цим терміном описується безліч методів обробки матеріалів, що ґрунтуються на зміні їх структури (і, відповідно, властивостей) під впливом температур. Часто у застосуванні до готового виробу все це часто називають "загартуванням", хоча власне загартування є лише одним із етапів. Іноді, приплітаючи сюди ще й гарячу деформацію, все це називають ТМО (термомеханічна обробка), що здебільшого докорінно невірно. Зазвичай термообробка включає кілька етапів (іноді - кілька десятків). Усі вони мають різні цілі та різні режими. Плутанини додає ще й те, що в теорії термічної обробки та на практиці досить часто окремі процеси мають різні назви залежно від мети та місця у технологічному циклі. Вдаватись у нетрі не будемо, нам скоріше важливі основні етапи та їх режими з погляду впливу на кінцевий результат.
Думаю, що буде простіше розібрати це на прикладі типової технології виробництва клинків (із зазначенням основних технологічних процесів), що застосовується переважною більшістю російських (та й світових теж) виробників. Розглянемо типову схему, що застосовується майстрами-приватниками та дрібносерійним виробником.
КУВАННЯ – один із видів оброблення металів тиском, який ґрунтується на здатності металів пластично деформуватися – змінювати форму, не руйнуючись, під дією зовнішніх сил. Куванню піддають метали та сплави, що мають досить високу пластичність і низький опір деформації. Під час кування здійснюють багаторазове переривчасте ударяння заготовки спеціальним інструментом. Зазвичай її встановлюють незакріпленою на ковадлі або в підкладеному штампі.
1. Нормалізація (іноді + висока відпустка)
(вирізання бланків)
2. Відпал чи ТЦО.
3. Загартування з МКО
4. Висока відпустка
5. Загартування
6. Кріообробка
7. Результуюча відпустка
(Чорнове шліфування)
8. Відпустка після шліфування
(чистове шліфування та доведення)
У випадку, якщо обробляється різанням, можуть бути додаткові відпустки (або відпали).
При масовому виробництві однакових деталей частіше застосовують штампування або пресування. Основні операції під час кування:
При осадженні матеріал розплющують – ширину та довжину збільшують, а товщину зменшують доти, поки йому не нададуть необхідних розмірів і форми;
При висадженні створюють потовщення внаслідок зменшення довжини. У процесі ручного або машинного кування. використовують основні, підтримуючі та вимірювальні інструменти.
- протягання,
- розкочування,
- прошивання,
- різання,
- згинання та виправлення.
Серед основних інструментів для ручного кування – кувалда, молотки, ручники, борідки, зубила, обтискачі, відбійники; серед основних машинних інструментів – бойки (плоскі, фасонні, заокруглені, комбіновані), плити, прошивні. Як підтримуючі інструменти при ручному куванні використовують кліщі, стояки, при машинному – кліщі, патрони. Заготовками для кування можуть бути зливки, сортовий і профільний прокат, листи та ін. Сталеві заготовки перед куванням переважно нагрівають в полуменевих або різного типу електричних печах до температури 1100–1250 °С.
Переваги оброблення металів куванням порівняно з різанням:
- менша (близько 30 %) витрата металу на виріб;
- вища продуктивність устаткування;
- метал стає щільнішим за своєю структурою.
Кування без нагрівання було відоме ще в часи пізнього неоліту, за допомогою нього здійснювали оброблення самородків металів (міді, золота, срібла, метеорит. заліза).
Розглянемо вплив окремих етапів на властивості та якість виробів.
1. Нормалізація (іноді + висока відпустка) – дозволяє привести структуру сталі "до спільного знаменника" від якого можна танцювати далі, зняти напруги, подрібнити зерно, в окремих випадках прибрати карбідну сітку або отримати необхідну для обробки твердість. Здійснюється у вигляді нагріву до температур вище температури фазових перетворень (часто до температур, що викликають помітне розчинення карбідів) та охолодження на спокійному повітрі. Багато стали при цьому здатні піджарюватися і отримувати високу твердість - у цьому випадку додають високу відпустку.
2. Відпал або ТЦО – Дозволяє подрібнити зерно, знизити твердість до мінімальних значень (для обробки різанням чи холодної деформації), зняти залишкову напругу. Здійснюється нагріванням до температур трохи вище температур фазових перетворень (в окремих випадках – міжкритичну область) і повільним охолодженням до температур закінчення перлітного розпаду. Часто відпал вигідно замінювати термоциклічною обробкою - багаторазовим повторенням циклів нагрівання-охолодження до температур відповідно вище/нижче температур фазових перетворень. Така обробка дозволяє помітно більшою мірою подрібнити зерно і в результаті отримати помітно найкраще хутро. Характеристики.
3. Загартування з МКО. Дозволяє значно зменшити повідці та короблення деталей, завдяки закриттю мікропор в окремих випадках дещо підвищує твердість та хутро. Показники сталей. Виконується як "м'яка" загартування з міжкритичної області, як правило, охолодженням в олії.
4. Висока відпустка (з погляду теорії ТО – докритичний відпал) – знімає напруги після хутра. обробки, що готує структуру сталі до загартування, в окремих випадках знижує твердість сталі до мінімальних значень.
5. Загартування - Основний етап ТО. Полягає в нагріванні до температур, вище температур фазових перетворень і як правило, що викликають помітне розчинення карбідів, що створюють необхідне насичення твердого розчину вуглецем і легуючими елементами та швидкому охолодженні (зі швидкістю вище критичної), що фіксують цей твердий пересичений розчин.
6. Кріообробка - охолодження виробу до низьких температур (як правило -78 - 196С). Мається на меті можливе повніше перетворення залишкового аустеніту, що збільшує твердість, стійкість до зминання і зменшує ризик перетворення аустеніту при експлуатації, але може знижувати в'язкість.
7. Результуюча відпустка – формує остаточні властивості клинка. Зазвичай здійснюють нагрівання до відносно невисоких температур (іноді середніх температур). При загартуванні на вт
8. Відпустка після шліфування - знімає шліфувальні напруги і іноді стабілізує аустеніт, що утворився при шліфуванні.
Не всі етапи не завжди необхідні, деякі можуть частково або повністю замінювати один одного – все залежить від сталі та технологічного циклу. У разі купівлі напівфабрикатів помітну частину ТО вже зроблено на підприємстві – виготовлювачі.
Зазвичай етапи ТО ділять на попередню та результуючу ТО. Результуюча ТО формує властивості готового виробу (як правило, це все, починаючи з останнього високотемпературного ступеня – загартування), завдання ПТО – забезпечити необхідні технологічні властивості та підготувати структуру до результуючої ТО.
Звичайно, саме результуюча ТО найбільше впливає на "базові" властивості сталі, але саме ПТО часто дозволяє "вичавити" зі сталі максимум того, на що вона здатна.
Звичайно - безкоштовних тістечок не буває. З ускладненням ТО зростають трудовитрати, завантаження устаткування тощо. Що неминуче призводить до зростання ціни виробів. Часто багаторазовому. Тому зайве оптимістично шукати діаманти серед ширвжитку. З іншого боку, спроби вичавити максимум можуть призвести до таких витрат, що виріб набуває статусу "ексклюзиву" з відповідною ціною. Треба десь зупиниться. Де саме – кожен виробник вирішує собі сам. Точніше – там, де зупиняється його цільовий покупець.
Розглянемо основні варіанти.
1. Скував, нагрів у горні до яскраво-жовтогарячого, засунув у масло. Потримав над вугіллям 5 хвилин - насельнику, все… У цьому випадку розраховувати хоча б на середній для цієї сталі результат досить оптимістично. При величезному досвіді можливо все…
2. Віддав "якомусь термісту" з оборонного заводу. Що і як той із залізницею робив – таємниця ця є велика… Результат – від повного відстою до дуже непогано, правда з помітною перевагою першого. Кадри вирішують усі.
3. Є грубка, є "даташит", є смужка буржуйської сталі. Знань та розуміння чого і як – ні. Якщо особливо сильно не косячити, то можна отримати хороший результат. Особливо із сучасними сталями – вони, як правило, досить толерантні до помилок.
4. Те саме + мінімальні уявлення про те, що, куди і навіщо. Як правило, при накопиченні та осмисленні власного та чужого досвіду та особистої відповідальності можливе отримання стабільно добрих результатів.
5. Є чіткі уявлення про предмет та/або величезний особистий досвід. Плюс зацікавленість у результаті та особиста відповідальність. Це передумови отримання стабільних результатів помітно вище середнього. Авторські схеми ТО часто дозволяють вичавити зі сталей помітно більше за те, чого від них чекають.
6. Клинки - чемпіони вимагають ще й деякої частки удачі.
Розглянемо основні помилки при ТО та їх вплив на якість виробу.
1. Недостатня твердість - як правило, наслідок недогріву при загартуванні (рідко - перегрівання) або надмірно високої відпустки. У помірних формах зустрічається на недорогих ножах як компенсатор надмірно спрощеної ТО.
2. Надмірна твердість та крихкість “Перекал”. А ось тут усе складніше. Часто йдеться не про високу твердість, а про перегрівання при загартуванні (або непроведеному ПТО), коли сталь отримує занадто велике зерно. Власне, твердість не є єдиним показником якості ТО – до однієї й тієї ж твердості можна прийти різними шляхами та з різним результатом. Так що твердження типу "Ніж вище 58HRc крихкий як скло" треба сприймати зі здоровим скепсисом.
3. Безвуглецевий шар. За відсутності захисних атмосфер/покриттів або вакуумного обладнання є практично завжди. При травленні зазвичай виглядає помітно світліше фону. При правильному плануванні техпроцесу цей шар видаляється, але в окремих випадках (наприклад, при загартуванні тонко зведеної заготівлі або виконання ножа зі "стамесочной" заточуванням без видалення обезуглероженного шару) він може виходити на РК, з найсумнішими наслідками для останньої. Іноді він може стати причиною помилок щодо твердості – там вона буде помітно менше ніж на тілі клинка і РК.
4. Тріщини. Можуть з'явитися на різних етапах виробництва, найчастіше при куванні, загартуванні чи шліфуванні. Є безумовним невиправним шлюбом. Продаж такого клинка (за винятком ДУЖЕ рідкісних випадків на багатошарових мечах або дамасках) - пряма вказівка на ставлення виробника до справи. Хрінове ставлення.
5. Поводки та короблення. На довгомірі вони практично неминучі, на короткому мечі допустимі до певної міри.
На закінчення кілька реальних історій про різні ножі.
1. Проводячи гарт коваль А свинчивает кілька десятків заготовок шпильками, кидає в піч, йде пити горілку. Через кілька годин повертається, кидає "бутерброд" у бак з маслом, йде пити горілку. Відпустки не робить – а навіщо там і так 58…
2. Коваль Б протягом багатьох років калить Х12МФ з температур на 50 градусів вище оптимальних. На резонне запитання про причини – “Я завжди так роблю, люди не скаржаться”.
3. Ентузіаст В вирішив провести кріообробку шляхом загартування розпеченої до 1175 р. заготівлі в рідкому азоті. На пропозицію спочатку знайти значення теплоти випаровування для рідкого азоту за два дні задумливо висловив “бля”.
4. Коваль Г калить кожну заготовку по-різному. При цьому сам їх не відчуває і систематично не збирає відгуки. Шукає людина…
5. Майстер Д при загартуванні КОЖНОГО клинка крім авторської ТО і перевірки на твердість завжди контролює злам - про всяк випадок. Ось це – заявка на відповідальне ставлення до справи, що проявляється в інших питаннях і знаходить свій відбиток у ціні виробів.
Так що, вибираючи ТО ви обираєте ВИРОБНИКА. У різних майстрів можуть бути різні погляди на ТО, але відповідальний і поважаючий себе і споживача виробник ніколи не випустить у продаж виріб з властивостями нижче за деякий мінімум. А у разі шлюбу (чого не буває) докладе максимум зусиль до вирішення ситуації.
Процеси термічної обробки сталі
Сталі можна піддавати термічній обробці для отримання широкого діапазону мікроструктур і властивостей. Як правило, термічна обробка використовує фазове перетворення під час нагрівання та охолодження для зміни мікроструктури твердого стану. При термічній обробці обробка, як правило, термічна і змінює лише структуру сталі. У разі термомеханічної обробки сталей форма і структура сталевих компонентів також змінюються. У разі термохімічної обробки сталей хімічний склад поверхні та структура сталі модифікуються. Процеси термомеханічної та термохімічної обробки також є важливими підходами до термічної обробки сталі, і вони розглядаються в області термічної обробки. Процес термічної обробки вимагає ретельного контролю за всіма факторами, що впливають на нагрівання та охолодження сталі. Атмосфера нагрівальної печі також впливає на стан сталі, що піддається термічній обробці.
Усі процеси термічної обробки складаються з піддавання сталі певному температурно-часовому циклу. Цей часово-температурний цикл складається з трьох компонентів, а саме (i) нагрівання, (ii) витримування в певному діапазоні температур (замочування) і (iii) охолодження. Окремі випадки можуть відрізнятися, але певні фундаментальні цілі є.
Швидкість нагріву деталі залежить від кількох факторів. Ці фактори: (i) теплопровідність сталі, (ii) стан сталі та (iii) розмір і поперечний переріз сталі. Важливим фактором є теплопровідність сталі. Сталь з високою теплопровідністю нагрівається швидше, ніж сталь з низькою теплопровідністю. Швидкість нагрівання не є особливо важливою, якщо тільки сталь не перебуває у стані сильного навантаження, наприклад, у результаті сильної холодної обробки або попереднього загартування. У таких випадках швидкість нагрівання повинна бути повільною. Часто це практично неможливо, оскільки печі, які використовуються для нагрівання, можуть мати робочу температуру, а розміщення холодної сталі в гарячій печі може спричинити деформацію або навіть розтріскування. Цю небезпеку можна звести до мінімуму, використовуючи піч попереднього нагріву, яка підтримується при температурі нижче температури A1 на фазовій діаграмі залізо-вуглець (рис. 1). Сталь, попередньо нагріта протягом достатнього часу, потім переміщується в піч, яка знаходиться при робочій температурі. Ця процедура також корисна при обробці сталей із значними коливаннями товщини профілю або дуже низькою теплопровідністю.
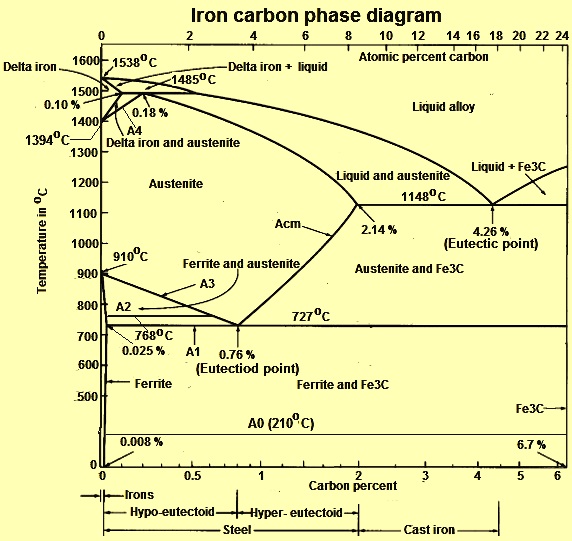
Рис. 1. Фазова діаграма залізо-вуглець
Після того, як сталевий профіль нагрівається до належної температури, його витримують при цій температурі, доки не відбудуться бажані внутрішні структурні зміни. Цей процес називається «замочування». Період витримки при належній температурі називається «періодом замочування». Завдання замочування - забезпечити рівномірність температури по всьому об'єму. Очевидно, що тонкі зрізи не потрібно замочувати так довго, як товсті зрізи, але якщо одна й та сама сталева деталь різної товщини, час, необхідний для рівномірного нагріву найтовстішого зрізу, вирішить час при температурі. Як правило, приблизно 30 хвилин замочування необхідно для зрізу товщиною 25 мм.
Після того, як сталевий профіль замочується, його потрібно повернути до кімнатної температури для завершення процесу термічної обробки. Для охолодження металу можна використовувати холодоагент. Охолоджувальне середовище може складатися з газу, рідини, твердої речовини або їх комбінації. Швидкість охолодження сталевого профілю залежить від сталі та бажаних властивостей. Швидкість охолодження залежить від охолоджувального середовища, а отже, вибір охолоджувального середовища має важливий вплив на необхідні властивості. Мікроструктура та властивості сталі залежать від швидкості охолодження сталі, а це, у свою чергу, визначається такими факторами, як маса, середовище для гарту тощо. Слід розуміти, що чим товщий профіль сталі, тим більше повільніша швидкість охолодження незалежно від використовуваного методу охолодження, за винятком таких операцій, як індукційне гартування.
Різні типи процесів термічної обробки схожі, оскільки всі вони включають нагрівання та охолодження сталі. Однак процеси відрізняються за використовуваними температурами нагрівання та швидкістю охолодження та кінцевими результатами. Нормальними процесами, що використовуються для термічної обробки сталі, є (i) відпал, (ii) нормалізація, (iii) загартування та (iv) відпуск.
Відпал
Відпал - це процес термічної обробки, який включає нагрівання та охолодження. Процес зазвичай використовується для розм’якшення сталі. Термін також відноситься до обробок, спрямованих на зміну механічних або фізичних властивостей, створення певної мікроструктури або видалення газів. Температура операції і швидкість охолодження залежать від типу сталі, що відпалюється, і мети обробки. Різні типи процесів відпалу описані нижче.
Повний відпал – це процес розм’якшення, під час якого сталевий профіль нагрівається до температури, що перевищує діапазон аустенітного перетворення, і після витримування протягом достатнього часу при цій температурі повільно охолоджується до температури, нижчої за діапазон перетворення. Сталі, як правило, дозволяють повільно охолонути в печі, хоча її можна вийняти та охолодити в якомусь охолоджуючому середовищі. Оскільки на температури перетворення впливає вміст вуглецю в сталі, очевидно, що високовуглецеві сталі можна повністю відпалити при нижчих температурах, ніж низьковуглецеві сталі. Мікроструктура доевтектоїдних сталей, які утворюються після повного відпалу, складається з фериту та перліту. Евтектоїдні та заевтектоїдні сталі часто частково або повністю сфероїдизуються при повному відпалі.
Технологічний відпал – технологічний відпал також часто називають відпалом для зняття напруги. Процес, як правило, використовується для холодної обробки сталі з низьким вмістом вуглецю (приблизно до 0,25 % вуглецю) для достатнього розм’якшення сталі для подальшої холодної обробки. Сталь зазвичай нагрівається близько до температури А1, але нижче її. Якщо сталь не підлягає подальшій холодній обробці, але потрібне зняття внутрішньої напруги, тоді достатнім є нижчий діапазон температур (приблизно 540 °C). Тут не важлива швидкість охолодження. Цей тип відпалу викликає рекристалізацію та розм’якшення холоднооброблених феритових зерен, але зазвичай не впливає на відносно невелику кількість холоднообробленого перліту.
Сфероїдизація
Сфероїдизація - це процес нагрівання та охолодження сталі, який утворює округлу або кулясту форму карбіду в матриці фериту. Зазвичай це здійснюється шляхом тривалого нагрівання при температурах трохи нижче температури A1, але його можна полегшити шляхом почергового нагрівання до температур трохи вище температури A1 та охолодження до температури трохи нижче A1. Останній етап, однак, складається з витримки при температурі трохи нижче критичної температури A1. Швидкість охолодження не є важливою після повільного охолодження приблизно до 540 °C. На швидкість сфероїдизації впливає початкова структура. Чим дрібніший перліт, тим легше відбувається сфероїдизація. Мартенситна структура дуже сприйнятлива до сфероїдизації. Ця обробка зазвичай використовується для високовуглецевих сталей (0,60 % вуглецю і вище). Метою цієї обробки є поліпшення оброблюваності сталі. Процес також використовується для кондиціювання високовуглецевої сталі для холодного витягування дроту.
Нормалізація
Нормалізована обробка часто застосовується до сталі для досягнення будь-якої однієї або кількох із цих цілей, а саме (i) для покращення зернистої структури, (ii) для отримання однорідної структури, (iii) для зменшення залишкових напруг та ( iv) покращити оброблюваність сталі.
Нормалізація - це процес, під час якого сталь нагрівають до температури, що перевищує температуру A3 або Acm, а потім охолоджують в атмосферному повітрі. Метою нормалізуючої обробки є усунення наслідків будь-якої попередньої термічної обробки (включаючи грубозернисту структуру, яка іноді є результатом високих температур кування) або холодної обробки. Процес нормалізації виконується для забезпечення однорідного аустеніту при повторному нагріванні для загартування або повного відпалу. Отримані структури є перлітовими або перлітовими з надлишком фериту або цементиту, залежно від складу сталі.
Структури після нормалізації відрізняються від структур, отриманих після відпалу, і сталей з однаковим вмістом вуглецю в заевтектоїдному або заевтектоїдному діапазонах, там менше надлишку фериту або цементиту, а перліт більш дрібний. Це результати більш швидкого охолодження. Оскільки на тип структури, а отже, і на механічні властивості впливає швидкість охолодження, у нормалізованих сталях можуть мати місце суттєві варіації через різницю в товщині перерізу форм, що нормалізуються.
Загартовування
Сталі можна загартувати простим засобом нагрівання сталі до температури, вищої за температуру перетворення А3, витримування достатньо довго, щоб забезпечити досягнення рівномірної температури та розчинення вуглецю в аустеніті, а потім швидке охолодження сталі (загартування). Повне зміцнення залежить від охолодження настільки швидко, що аустеніт, який не розкладається при охолодженні через температуру А1 і підтримується при відносно низьких температурах. Коли це досягається, аустеніт починає перетворюватися на мартенсит при охолодженні нижче температури Ms (приблизно 220 °C) і повністю перетворюється на мартенсит нижче температури Mf. Швидке охолодження необхідне лише для того, щоб температура сталі знизилася значно нижче верхньої частини S-кривої (рис. 2). Коли це досягнуто, повільне охолодження з цього моменту, або в маслі, або на повітрі, є корисним для уникнення деформації та розтріскування. Спеціальні методи обробки, такі як загартування з часом і загартування, призначені для досягнення цих умов. Оскільки мартенсит досить крихкий, сталь рідко використовують у загартованому стані, тобто без відпустки. Максимальна твердість, якої можна досягти в повністю загартованих низьколегованих сталях і простих вуглецевих конструкційних сталях, залежить в першу чергу від вмісту вуглецю.
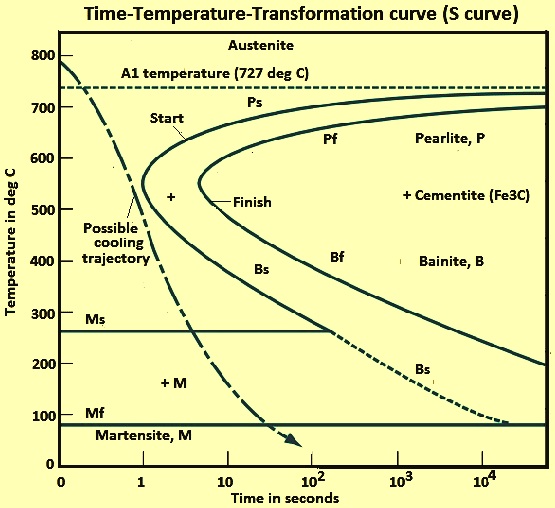
Рис. 2 Крива перетворення час-температура
Вплив маси – маса сталі впливає на формування мартенситу. Видно, що навіть при відносно невеликих розмірах зразка швидкість відведення тепла нерівномірна. Тепло завжди видаляється з поверхневих шарів швидше, ніж із внутрішнього зілля. У даному охолоджувальному середовищі швидкість охолодження як поверхні, так і внутрішньої частини зменшується зі збільшенням розмірів зразка, і можливість перевищення критичної швидкості охолодження стає меншою. Щоб подолати це, сталь потрібно загартувати в середовищі, яке має дуже високу швидкість відведення тепла, наприклад, охолодженому розсолі, але, незважаючи на це, багато сталей мають фізичне обмеження на максимальний розмір, чутливий до повного загартування незалежно від цього. середовища гасіння. Помітний вплив маси на твердість загартованої сталі можна продемонструвати, вимірявши розподіл твердості різних за розміром заготовок тієї самої сталі, загартованої в одному середовищі.
Вплив вуглецю – Вміст вуглецю в простих вуглецевих і низьколегованих сталях впливає на температуру перетворення Ms. Зі збільшенням вмісту вуглецю температура Ms знижується (рис. 3).
Рис. 3 Вплив вуглецю на температуру Ms
Загартовування
Відпуск (іноді його називають витягуванням) — це процес повторного нагріву загартованої (мартенситної) або нормалізованої сталі до температури, нижчої за температуру А1. Швидкість охолодження не має значення, за винятком деяких сталей, які чутливі до відпускної крихкості. У міру підвищення температури відпуску мартенсит загартованої сталі проходить через стадії відпущеного мартенситу і поступово перетворюється на структуру, що складається із сфероїдів цементиту в матриці фериту (раніше називався сорбіт). Ці зміни супроводжуються зменшенням твердості та підвищенням ударної в'язкості.
Температура відпуску залежить від бажаних властивостей і мети, для якої буде використовуватися сталь. Якщо необхідна значна твердість, то температура відпустки має бути низькою. З іншого боку, якщо потрібна значна в'язкість, то температура відпустки має бути високою. Правильний відпуск загартованої сталі вимагає певного часу. При будь-якій обраній температурі відпустки твердість спочатку швидко падає, поступово зменшуючись повільніше в міру продовження часу. Короткі періоди загартовування зазвичай небажані, тому їх слід уникати. Хороша практика вимагає принаймні 30 хвилин (або краще 1-2 години) при температурі відпуску для будь-якої загартованої сталі.
Неможливо переоцінити необхідність гартування сталі відразу після загартування. Якщо повністю загартована сталь охолоне до кімнатної температури під час гартування, існує небезпека розтріскування сталі. Вуглецеві сталі та більшість низьколегованих сталей потрібно відпускати, як тільки вони достатньо охолонуть, щоб їх було зручно тримати в руках. Сталі не можна відпускати до того, як вони охолонуть до цієї температури, оскільки в деяких сталях температура Mf досить низька і може бути присутнім неперетворений аустеніт. Частина всього цього залишкового аустеніту перетворюється на мартенсит при охолодженні від температури відпуску, так що кінцева структура складається як з відпущеного, так і з невідпущеного мартенситу. Крихкий невідпущений мартенсит разом із внутрішніми напругами, викликаними його утворенням, можуть легко спричинити руйнування термічно обробленої сталевої деталі. Якщо можливо, що така умова існує, необхідно провести другий відпуск (подвійний відпуск) для відпустки свіжого мартенситу, який утворився при охолодженні після початкового відпуску.
Якщо конструкційні сталі повинні використовуватися в нормалізованому стані, операція нормалізації часто супроводжується нагріванням до температури приблизно від 650 °C до 700 °C. Метою цієї обробки, яка також позначається як відпуск, є звільнення внутрішньої напружень, що виникають при охолодженні від температури нормалізації, і для поліпшення пластичності сталі.
Зміцнення корпусу
Загартування цементу - це процес загартування чорних сплавів таким чином, що поверхневий шар або корпус стає значно твердішим, ніж внутрішній шар або сердечник. Хімічний склад поверхневого шару змінюється під час обробки додаванням вуглецю, азоту або обох. Найпоширенішими процесами цементування є науглерожування, ціанування, карбоназотування та азотування.
Цементація – це процес, який вводить вуглець у твердий сплав заліза шляхом нагрівання металу в контакті з вуглецевим матеріалом до температури, що перевищує температуру A3 сталі, і витримування при цій температурі. Глибина проникнення вуглецю залежить від температури, часу перебування при температурі та складу цементуючого агента. Як приблизний показник, глибина науглерожування приблизно від 0,75 мм до 1,25 мм може бути досягнута приблизно за 4 години при 930 °C, залежно від типу науглерожувача, який може бути твердим, рідким або газоподібним. Оскільки основною метою науглерожування є отримання твердого корпусу та відносно м’якого, міцного сердечника, використовуйте лише низьковуглецеві сталі (максимум приблизно 0,25 % вуглецю), з легуючими елементами (нікель, хром, марганець) або без них. або молібден), зазвичай використовуються. Після цементації сталь має високовуглецевий корпус, що переходить у низьковуглецеве ядро.
Після науглерожування можна використовувати різноманітні термічні обробки, але всі вони включають загартування сталі для зміцнення науглерожуваного поверхневого шару. Найпростіша обробка полягає в загартуванні сталі безпосередньо від температури цементації. Ця обробка зміцнює як корпус, так і сердечник (наскільки сердечник можна загартувати). Інша проста обробка, і, мабуть, найбільш часто використовувана, полягає в повільному охолодженні від температури науглерожування, повторному нагріванні до температури вище A3 корпусу (приблизно 775 °C) і гарту. Така обробка тільки зміцнює корпус. Більш складна обробка полягає в подвійному гарту, що складається з першого гарту вище температури A3 серцевини (приблизно 900 °C для низьковуглецевої сталі), а потім від температури вище A3 корпусу (близько 775 °C). Ця обробка очищає сердечник і зміцнює корпус. Звичайні вуглецеві сталі майже завжди гартуються у воді або розсолі, тоді як леговані сталі зазвичай гартуються в олії.
Хоча відпуск після загартування цементованої сталі іноді пропускають, низькотемпературний відпуск приблизно при 300 °C є хорошою практикою. Іноді бажано науглерожувати лише окремі частини поверхні. Це можна зробити, покривши поверхню, яку потрібно захистити від науглерожування, деяким матеріалом, який перешкоджає проходженню науглерожувача. Найпоширенішим методом є міднення поверхонь, що захищаються. Також доступні кілька запатентованих розчинів або паст, які досить ефективно запобігають науглерожуванню. Комерційні суміші, які зазвичай використовуються для пакувального (твердого) цементування, містять суміші карбонату (зазвичай карбонату барію), коксу (розріджувач) і деревного вугілля з листяних порід із олією, смолою або патокою як сполучною речовиною. Використовуються також суміші обвугленої шкіри, кістки та деревного вугілля. Науглерожуюча дія цих сполук зменшується під час використання, тому перед повторним використанням суміші необхідно додати новий матеріал. Додавання однієї частини невикористаної суміші до трьох-п'яти частин використаної суміші є звичайною практикою.
Деталі, які підлягають науглерожуванню, упаковують у ящики (або інші відповідні контейнери), виготовлені з жаростійких сплавів, хоча також можна використовувати прокат або литу сталь, де довговічність ящика неважлива. Верхню кришку коробки потрібно закрити шамотною глиною або іншим вогнетривким матеріалом, щоб запобігти витоку науглерожувального газу, який утворюється при температурі науглерожування. На глибину і однорідність корпусу впливає спосіб упаковки і конструкція тари. Рідке цементування складається з загартування сталі або чавуну в розплавлених соляних ваннах, які містять суміші в основному ціанідів (дуже отруйних), хлоридів і карбонатів. Корпус, отриманий цим методом, містить як вуглець, так і азот, але головним чином перший. Використовувані температури коливаються від приблизно 850 °C до 900 °C або вище, залежно від складу ванни та бажаної глибини корпусу. При 900 °C глибину корпусу приблизно від 0,25 мм до 0,4 мм можна досягти за 1 годину, а приблизно від 0,5 мм до 0,75 мм можна досягти за 4 години. Значно глибші корпуси можуть бути отримані при більш високих температурах з довшими періодами часу.
Після науглерожування сталь необхідно загартувати так само, як і під час твердого науглерожування, але зазвичай це робиться безпосередньо з розплавленої ванни. У всіх сучасних комерційних газових цементаціях два або більше вуглеводнів використовуються в комбінації для подачі вуглецю в сталь. В якості вуглеводнів використовуються метан, етан, пропан і пари нафти. Сталеві деталі поміщені в герметичні контейнери, через які циркулюють науглерожуючі гази. Використовувані температури знаходяться в районі 925 °C. Середнє очікуване значення глибини корпусу в науглерожуваній сталі наведено на рис. 4. Після науглерожування сталь підлягає загартуванню.
Рис. 4. Зв’язок часу та температури з проникненням вуглецю під час газового науглерожування
Ціанування – твердий, поверхневий корпус можна швидко отримати на низьковуглецевих сталях шляхом ціанування. Цей процес передбачає введення як вуглецю, так і азоту в поверхневі шари сталі. Сталь, яка підлягає ціанідуванню, зазвичай нагрівають у розплавленій ванні ціанід-карбонат-хлоридних солей (зазвичай містить від 30 % до 95 % ціаніду натрію), а потім гартують у розсолі, воді або мінеральному маслі. Робоча температура зазвичай знаходиться в діапазоні від 850 °C до 875 °C. Глибина корпусу залежить від часу, температури та складу ціанідної ванни. Час занурення відносно короткий у порівнянні з науглерожуванням, зазвичай варіюється від 15 хвилин до 2 годин. Максимальна глибина корпусу рідко перевищує приблизно 0,5 мм, а середня глибина значно менша.
Ціанідувати сталі можна також шляхом нагрівання до відповідної температури та занурення в порошкоподібну ціанідну суміш або посипання порошку на сталь з подальшим гартуванням. Сформований таким чином корпус надзвичайно тонкий. Ціанідуючі солі надзвичайно отруйні, якщо потрапити на подряпини або рани. При прийомі всередину вони смертельно отруйні. При контакті ціанідів з кислотами виділяються смертельно отруйні пари. Ванни ціанування повинні бути обладнані ковпаком для відводу газів, що виділяються при нагріванні, а робоче приміщення повинно добре провітрюватися. Ніколи не можна допускати контакту розплавленого ціаніду з нітратами натрію або калію, які зазвичай використовуються для ванн для гарту, оскільки суміші вибухонебезпечні. Крім того, необхідна обережність при підготовці соляної ванни, і сталь повинна повністю висохнути перед розміщенням у розплавленій ванні. При експлуатації та обслуговуванні соляних ванн необхідно суворо дотримуватися рекомендацій виробників солі.
Карбонітридування – карбонітридування також відоме як газове ціанідування, сухе ціанідування та ні-карбінгування. Це процес загартування сталевої деталі в газовій атмосфері, яка містить аміак у контрольованих відсотках. Карбонітрування використовується в основному як недорогий замінник ціанування. Як і в процесі ціанування, до сталі додають вуглець і азот. Процес виконується вище температури A1 сталі та практичний до 925 °C. Загартування в маслі досить швидке для досягнення максимальної твердості поверхні. Така помірна швидкість охолодження мінімізує спотворення. Глибина, на яку проникають вуглець і азот, залежить від температури та часу. Проникнення вуглецю приблизно таке ж, як і при газовому науглерожуванні (рис. 3).
Азотування – Процес азотування полягає в піддаванні механічно обробленої та термічно обробленої сталі без зневуглецювання поверхні дії азотистого середовища, зазвичай газоподібного аміаку, при температурі приблизно від 500 °C до 540 °C. Дуже тверда поверхня є отримані цим процесом. Ефект поверхневого зміцнення зумовлений поглинанням азоту, тому подальша термообробка сталі відпадає. Необхідний час відносно тривалий, зазвичай становить від 1 до 2 днів. Корпус, навіть після 2 днів азотування, як правило, менше 0,5 мм. І найвища твердість існує в поверхневих шарах на глибину лише в кілька сотих міліметра.
Для азотування розроблені спеціальні низьколеговані сталі. Ці сталі містять елементи, які легко сполучаються з азотом з утворенням нітридів. Найбільш сприятливими з цих елементів є алюміній, хром і ванадій. Молібден і нікель використовуються в цих сталях для додання міцності та в'язкості. Зазвичай вміст вуглецю становить від 0,20% до 0,50%, хоча в деяких сталях, де необхідна висока твердість серцевини, він може досягати 1,3%. Нержавіючі сталі також можна піддавати азотуванню.
Оскільки азотування здійснюється при відносно низькій температурі, в якості основного матеріалу доцільно використовувати загартовану та відпущену сталь. Це дає міцну, міцну серцевину з інтенсивно твердим зносостійким корпусом, який справді є набагато твердішим, ніж можна отримати шляхом загартування карбонізованої або ціанідованої сталі. Хоча викривлення не є проблемою під час азотування, сталі трохи збільшуються в розмірі під час цієї обробки. Цей ріст можна врахувати в готовому виробі. Захист від азотування може бути досягнуто лудінням, мідненням, бронзуванням або нанесенням деяких фарб.
Поверхневе зміцнення
Часто доводиться зміцнювати тільки поверхню сталей без зміни хімічного складу поверхневих шарів. Якщо сталь містить достатню кількість вуглецю, щоб реагувати на загартування, можна зміцнити поверхневі шари лише дуже швидким нагріванням протягом короткого періоду часу, таким чином підготувавши поверхню для зміцнення шляхом загартування.
Індукційне гартування – під час індукційного гартування струм високої частоти пропускається через котушку, що оточує сталь, поверхневі шари якої нагріваються електромагнітною індукцією. Глибина, на яку поширюється нагріта зона, залежить від частоти струму (нижчі частоти дають більшу глибину) і від тривалості циклу нагрівання. Час, необхідний для нагрівання поверхневих шарів до температури вище A3, напрочуд малий і часто становить лише кілька секунд. Вибіркове нагрівання (і, отже, зміцнення) досягається відповідною конструкцією котушок або індукторних блоків. В кінці циклу нагрівання сталь зазвичай гартують струменями води, що проходять через котушки індуктора. Необхідні точні методи керування роботою, тобто витратою енергії, тривалістю нагрівання та швидкістю охолодження. Ці функції включені в обладнання для індукційного загартування, яке зазвичай працює повністю автоматично.
Гартування полум’ям – це процес нагрівання поверхневих шарів сталі вище температури перетворення за допомогою високотемпературного полум’я з подальшим гартуванням. Під час цього процесу полум’я газу потрапляє безпосередньо на сталеву поверхню, яку потрібно загартувати. Швидкість нагрівання дуже висока, хоча й не така швидка, як при індукційному нагріванні. Звичайні вуглецеві сталі зазвичай гартують розбризкуванням води, тоді як швидкість охолодження легованих сталей може варіюватися від швидкого гарту водою до повільного охолодження повітрям залежно від складу. Будь-який тип загартованої сталі можна загартувати полум'ям. Для досягнення найкращих результатів вміст вуглецю має становити щонайменше 0,35 %, звичайний діапазон становить від 0,40 % до 0,50 %.
Спеціальні процеси обробки
Спеціальні процеси обробки зазвичай включають відпуск, відпуск і холодну обробку
Austempering – Austempering – це торгова назва запатентованого процесу термічної обробки. В основному він складається з нагрівання сталі до температури перетворення вище A3, а потім загартування в гарячій ванні, що підтримується при температурі, нижчій від тієї, при якій утворюється дрібний перліт (кінець S-кривої, рис. 2), але вище температури Ms. як показано на рис. 3. Продуктом ізотермічного розкладання аустеніту в цій температурній області є бейніт. Цей компонент поєднує в собі відносно високу в'язкість і твердість.
Процес відпустки має певні обмеження, які роблять його неможливим для використання з багатьма сталями. Щоб забезпечити однорідну структуру (і, отже, однорідні властивості), важливо, щоб весь поперечний переріз сталі досить швидко охолоджувався, щоб навіть центр уникнув трансформації в кінці S-кривої. У вуглецевих сталях час, необхідний для початку перетворення в кінці S-кривої, є надзвичайно коротким, тому лише відносно невеликі секції (близько 10 мм максимальної товщини) можуть бути успішно загартовані гарячим способом у ваннах аусгарту. Час, необхідний для перетворення аустеніту легованих сталей на тонкодисперсний перліт, як правило, довший, і, отже, більші секції можна успішно піддати аустемперації (близько 25 мм максимум). Однак час, необхідний для перетворення в бейніт, часто стає надмірно довгим для багатьох легованих сталей, і, отже, процес відпустки зазвичай неможливий для цих сталей.
Загартування – Загартування складається з нагрівання сталі до температури перетворення вище A3, а потім загартування у ванні, що підтримується при температурі, яка приблизно дорівнює температурі Ms. Сталь витримують у гарячій ванні, поки її температура не стане рівномірною, а потім її охолоджують на повітрі. Під час гартування в сталі виникають сильні внутрішні напруги. Під час охолодження сталь стискається, але піддається помітному розширенню, коли аустеніт перетворюється на мартенсит. Оскільки загартована сталь повинна охолоджуватися від поверхні всередину, різні частини перетворюються в різний час. Таким чином, сталь піддається різноманітним різним розширенням і звуженням, що призводить до значних внутрішніх напруг. Завдяки вирівнюванню температури по всій секції перед перетворенням, а потім повільному охолодженню через діапазон мартенситу (Ms-Mf), внутрішні напруги значно зменшуються, що також є основною метою відпуску.
Холодна обробка – температура Mf багатьох легованих сталей настільки низька, що повне перетворення аустеніту в мартенсит не відбувається під час загартування до кімнатної температури або охолодження після відпустки. Цей утриманий аустеніт може бути частково або повністю перетворений шляхом охолодження нижче атмосферної температури, і така обробка називається «холодною обробкою». Корисні ефекти лікування холодом до кінця не вивчені. Відомо, що залишковий аустеніт високолегованих сталей часто важко трансформувати. Охолодження цих сталей до низьких температур (до температури твердого СО2 або навіть нижче) одразу після загартування іноді є ефективним для перетворення залишкового аустеніту, але з пов’язаною з цим небезпекою розтріскування. Коли холодну обробку застосовують після відпустки, збережений аустеніт є значно більш стійким до перетворення. Якщо використовується холодна обробка, після цього сталь завжди має бути загартована.
Повторне почергове нагрівання до температури, трохи нижчої за ту, що використовується при гарту, і охолодження до мінусової температури в охолодженому розсолі з льодом, вуглекислий газ, рідке повітря або рідкий азот зазвичай використовуються для перетворення залишкового аустеніту (стабілізація розмірів) сталевих калібрів, особливо шарикопідшипникового типу.